RIECO
ELECTROSTATIC PRECITATORS
BAG FILTERS/BAG HOUSES
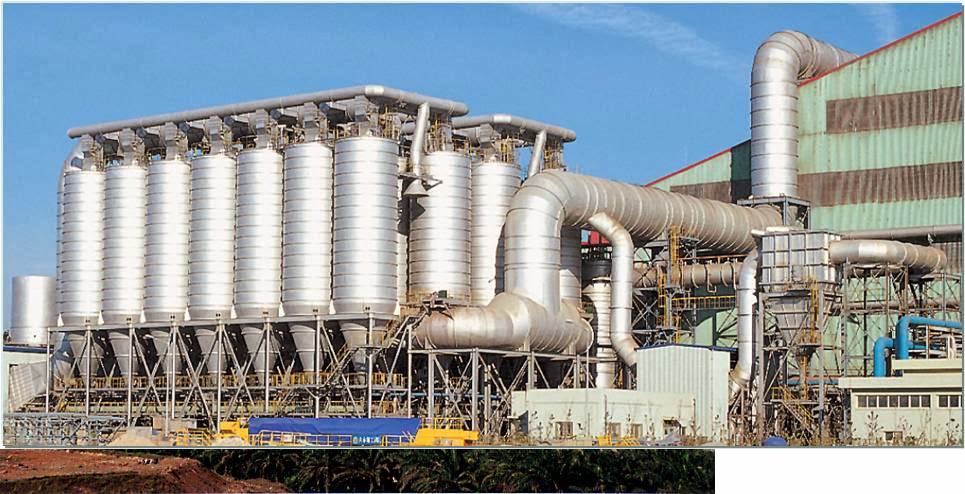
The Bag house used for the fume extraction in Steel Plant have very specific design considering all parameters used in processing of the steel.
Most baghouses use long, cylindrical bags (or tubes) made of woven or felted fabric as a filter medium. (For applications where there is relatively low dust loading and gas temperatures are 250°F or less, pleated, nonwoven cartridges are sometimes used as filtering media instead of bags.).Dust-laden gas or air enters the baghouse through hoppers (large funnel-shaped containers used for storing and dispensing particulate) and is directed into the baghouse compartment. The gas is drawn through the bags, either on the inside or the outside depending on cleaning method, and a layer of dust accumulates on the filter media surface until air can no longer move through it. When sufficient pressure drop (delta P) occurs, the cleaning process begins. Cleaning can take place while the baghouse is online (filtering) or is offline (in isolation). When the compartment is clean, normal filtering resumes.
Baghouses are very efficient particulate collectors because of the dust cake formed on the surface of the bags. The fabric provides a surface on which dust collects through the following four mechanisms:
ELECTROSTATIC PRECITATORS
FOB* Price: | US $ / Set | get the latest price |
---|---|
Min.Order Quantity: | 1 Set/Sets |
Payment Terms: | L/C,T/T, |
The design of Electrostatic Precipitators is typically based on customer specifications: they include expected performances under different operating conditions of the industrial process. The design analysis starts from these operating conditions, to choose one or two worst cases: then the main geometrical and electrical characteristics of the ESP are defined by use of simplified collection efficiency calculations, basically derived by the manufacturer empirical measurements and experience.
This paper will illustrate the example of a real industrial Electrostatic Precipitator designed by Area Impianti and IRS for a Glass Factory.
The worst case main operating conditions are reported in
table 1: the customer specifications require a particle density at the ESP outlet lower then 30 mg/Nm3(dryat 8% of O2). The particle size distribution is characterised by a double distribution:
fine particles from the furnace, and course particles from the process reactions with
the additives. The ESP draft characteristics are reported in the second part of table 1.
FLUE GAS OPERATING CONDITIONS |
Gas flow (on wet) | Nm3/h | 124000. |
Operating temperature | C | 402. |
Operating Pressure | KPa | 98.7 |
O2Concentration
| %vol | 11.25 |
Relative humidity | %vol | 8.7 |
INLET PARTICLE CHARACTERISTICS |
Particle concentration (dry at 8% O2)
| mg/Nm3 | 4707 |
Furnace particles (average diameter 0.25micron) | % in weight | 4.2 |
Reaction particles (average diameter 6.0 micron) | % in weight | 95.8 |
DRAFT ESP CHARACTERISTICS |
N° of fields | Nos. | 3 |
N° of gas passages ( d = 400 mm) | Nos. | 19 |
N° of plates per field ( h = 13.35 m, l = 0.5 m) | Nos. | 8 |
N° of emitting electrodes per plate (RDE type) | No. | 1 |
BAG FILTERS/BAG HOUSES
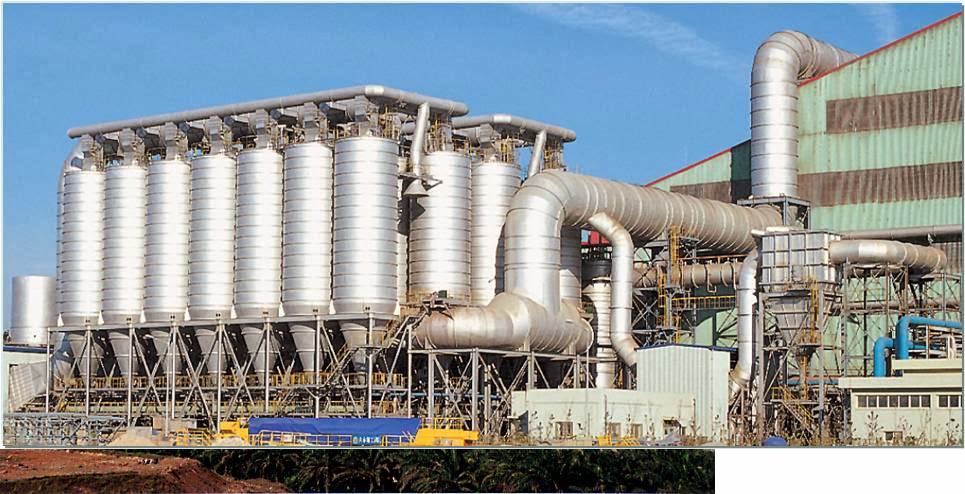
The Bag house used for the fume extraction in Steel Plant have very specific design considering all parameters used in processing of the steel.
Most baghouses use long, cylindrical bags (or tubes) made of woven or felted fabric as a filter medium. (For applications where there is relatively low dust loading and gas temperatures are 250°F or less, pleated, nonwoven cartridges are sometimes used as filtering media instead of bags.).Dust-laden gas or air enters the baghouse through hoppers (large funnel-shaped containers used for storing and dispensing particulate) and is directed into the baghouse compartment. The gas is drawn through the bags, either on the inside or the outside depending on cleaning method, and a layer of dust accumulates on the filter media surface until air can no longer move through it. When sufficient pressure drop (delta P) occurs, the cleaning process begins. Cleaning can take place while the baghouse is online (filtering) or is offline (in isolation). When the compartment is clean, normal filtering resumes.
Baghouses are very efficient particulate collectors because of the dust cake formed on the surface of the bags. The fabric provides a surface on which dust collects through the following four mechanisms:
- Inertial collection - Dust particles strike the fibers placed perpendicular to the gas-flow direction instead of changing direction with the gas stream.
- Interception - Particles that do not cross the fluid streamlines come in contact with fibers because of the fiber size.
- Submicrometre particles are diffused, increasing the probability of contact between the particles and collecting surfaces.
- Electrostatic forces - The presence of an electrostatic charge on the particles and the filter can increase dust capture.
- PNEUMATIC CONVEYING SYSTEM
- SIZE REDUCTION EQUIPMENTS
No comments:
Post a Comment